Rubber Compression Molding
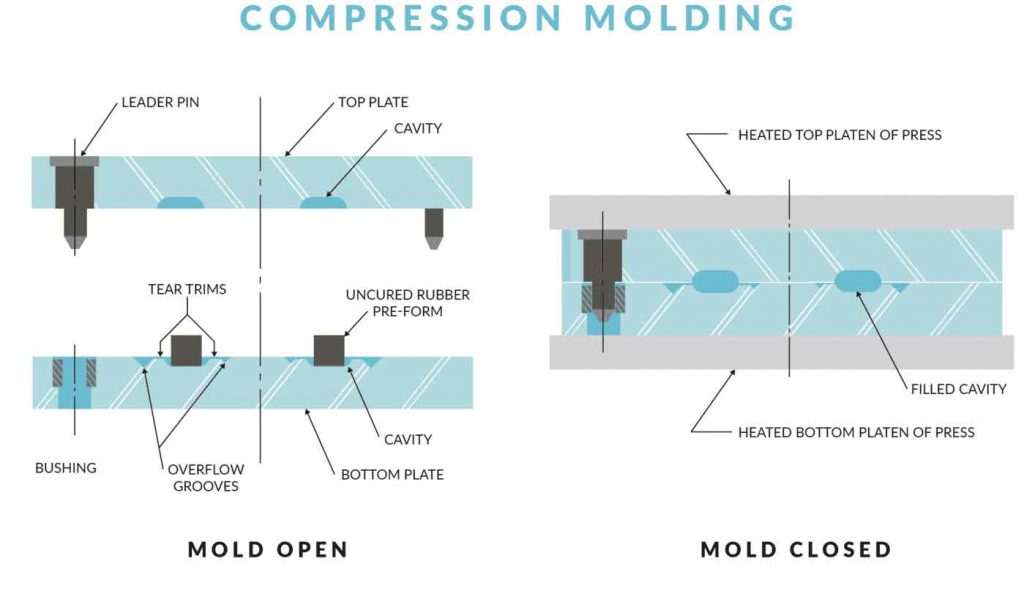
TECHNICAL DESCRIPTION
The sequence for compression molding rubber is identical to compression molding plastic except that the cycle time is slightly longer. To show the different compression molding techniques, a sheet geometry has here been used instead of a side action tool.
In stage 1, the rubber is conditioned to remove any crystallinity that might have built up since its production. Then a measure of conditioned rubber is placed in the lower mold. In stage 2, the 2 halves of the mold are brought together and pressure is applied gradually to encourage the material to flow. After 10 minutes the rubber is fully cured and its molecular structure is formed. In stage 3, the molds separate and the parts are peeled from the die cavity. The tear lines, which are integrated into the design to reduce secondary operations, ensure that the flash separates in a consistent manner when it is removed and so leaves a tidy edge detail.
INTRODUCTION
This process is used to mold rubber and plastic into sheet and bulk geometries. It is suitable for molding both thermosoftening and thermosetting materials. It is also used to produce parts in the dough and sheet molding compound (DMC and SMC), in DMC and SMC molding.
Compression molding thermosetting plastics has played an important role in the transition between metal and plastic parts in engineering. Plastics have been used to replace metals ever since phenolic resin (Bakelite) was first compression molded in the 1920s. Bakelite marks a significant point in the history of plastic manufacturing because it was the first synthetically produced polymer that could be molded. Since then, huge developments in plastic technology have meant that injection molding is now used to produce parts that were traditionally compression molded. Even so, compression molding is used to form certain rubber and thermosetting plastic parts that are not suitable for injection molding. DMC and SMC molding technologies followed in the 1960s and provided the industry with thermosetting plastic parts that compete with metal die castings in terms of strength, durability, and resilience.
The process of compression molding is simple: a measure of material is placed in between preheated matched tools, which come together and force the material into the die cavity.
TYPICAL APPLICATIONS
Compression molding is reserved for specific materials with particularly demanding applications such as heat and electrical insulation. Some typical applications include electrical housing, kitchen equipment, ashtrays, handles and light fittings. Demand has recently increased for under-the-bonnet applications in battery-powered cars because thermosetting materials can provide the electrical insulation and stability that are required for these parts.
Thermosetting rubber can be formed by compression molding, injection molding and vacuum casting. It is used to produce an array of products including flexible keyboards, keypads, seals and gaskets. Logos and other decorative moldings for running shoes, shoe soles and other sports equipment are also made in this way. Electronics housing can be molded in a single piece of rubber, which provides protection against damage as well as water. This is especially useful for handheld navigation devices and other portable electronic equipment.
QUALITY
This is a high quality process. Many of the characteristics can be attributed to the materials, such as heat resistant and electrically insulating phenolics or flexible and resilient silicones. Thermosetting plastics are more crystalline and so are more resilient to heat, acids and other chemicals.
The surface finish and reproduction of details are very good. By compressing rather than injecting material in the die cavity, the parts have reduced stress and are less prone to distortion.
COMPATIBLE MATERIALS
Compatible thermosetting materials include phenolic, polyester, urea, melamine and rubber. Even though it is possible to compression mold thermoplastics it is not recommended. There are many rubbers that can be molded in this way. The most common are silicones because they are readily available in small and large batches and take color very well.
COSTS
Tooling costs are moderate and much less expensive than for injection molding, especially for certain rubber sheet geometries, which can be made using simple and inexpensive tooling that is manually operated. For plastics, cycle time is very rapid and usually about 2 minutes per part. By contrast, rubbers take considerably longer and often need to be left in the heated press for 10 minutes or more.
Labor costs can be quite high.
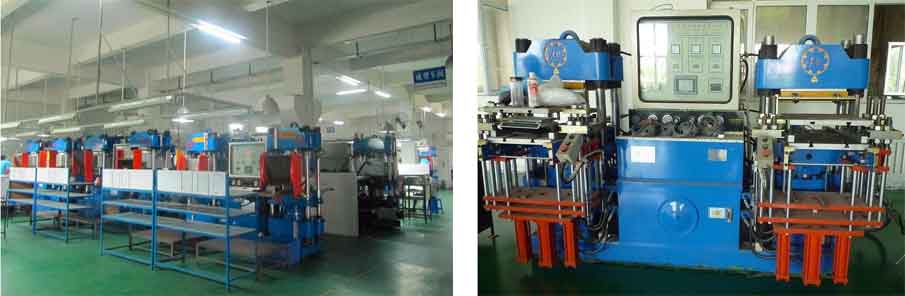