Sheet Metal Stamping
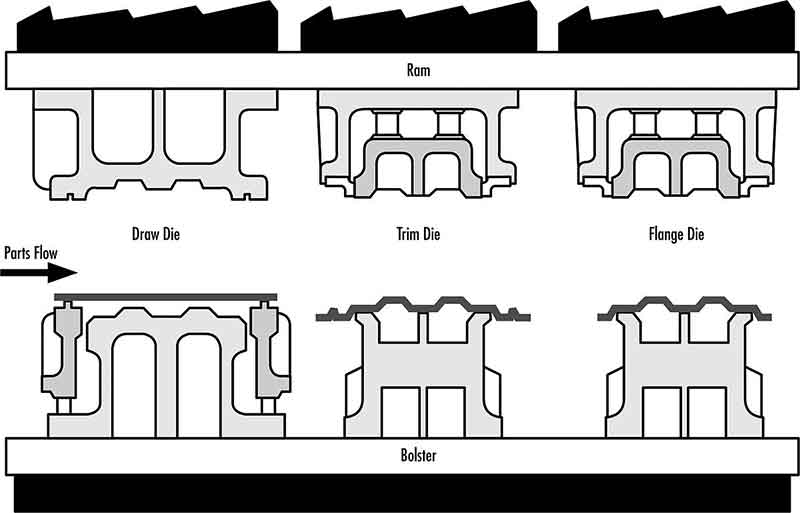
TECHNICAL DESCRIPTION
Metal stamping is carried out on a punch press. The power is transferred to the punch by either hydraulic rams or mechanical means such as a fly press. Hydraulic rams are generally preferred because they supply even pressure throughout the stamping cycle. Even so, fly presses still have their place in the metalworking industry.
The punch and die (matched tooling) are dedicated and generally carry out a single operation such as forming or punching. In operation, the metal blank is loaded onto the stripper. The punch then clamps and forms the part in a single stroke.
After forming, the stripper rises up to eject the part, which is removed. Sometimes the part is formed in a continuous strip, out of which it then has to be punched. This is common in progressive die forming.
In progressive die forming the stamped metal workpiece would now be transferred to the next workstation. This is either carried out manually, or by a transfer yoke. Most systems are automated for very high-speed production. The next operation may be further pressing, punching, beading or another secondary operation.
INTRODUCTION
Metal stamping is used to describe forming shallow metal profiles between matched steel tools. Tooling costs are high and so this process is only suitable for high volume production. It is a rapid process used to form precise shapes without significantly reducing the material’s thickness. It is known as deep drawing when the relationship between depth and diameter means that controlled drawing is required, which slightly reduces the material’s thickness during forming. Mass produced parts that require multiple forming and cutting operations are produced with progressive dies, a process made up of a series of dies working very rapidly and in tandem. While a part is being formed the second operation is being carried out simultaneously on the part that was formed previously and so on. Parts may require 5 operations or more, which is reflected in the number of workstations.
TYPICAL APPLICATIONS
Stamping is widely used. Most mass production metalwork in the automotive industry is stamped or pressed. Examples include bodywork, door linings and trim. Metal camera bodies, mobile phones, television housing, appliances and MP3 players are formed by stamping. Kitchen and office equipment, tools and cutlery are made in this way. Not only are the external features stamped, but also much of the internal metalwork and structure is shaped in the same way.
QUALITY
Shaped metal profiles combine the ductility and strength of metals in parts with improved rigidity and lightness. If appearance is not critical, parts are simply deburred after forming. Polishing is used to improved surface finish. Parts can also be powder coated, spray painted or electroplated.
DESIGN CONSIDERATIONS
Stamping is carried out on a vertical axis. Therefore, re-entrant angles have to be formed with a secondary pressing operation. Secondary operations include further press forming, cutting, deburring and edge rolling. The first stamping operation can only reduce the diameter of the blank by up to 30%. Subsequent operations can reduce the diameter by 20%. This indicates the number or operations (workstations) required in the production of a part. As in deep drawing, the limits of this process are often determined by the capabilities of the machine; bed size determines the size of blank and stroke determines the length of draw achievable. Speed is determined by stroke height and the complexity of the part. The thickness of stainless steel that can be stamped is generally between 0.4 mm and 2 mm (0.02-0.08 in.). It is possible to stamp thicker sheet, up to 6 mm (0.236 in.), but this will affect the shape that can be formed.
COMPATIBLE MATERIALS
Most sheet metals can be formed in this way including carbon steel, stainless steel, aluminium, magnesium, titanium, copper, brass and zinc.
COSTS
Tooling costs are high because tools have to be machined precisely from high-strength tool steel. Semi-rigid rubber tooling is less expensive, but still requires a single-sided steel tool and is only capable of low volume production. Cycle time is rapid and ranges from 1 to over 1oo parts per minute. Changeover and setup can be time consuming. Labor costs are generally low because this process is mechanized and often fully automated. Finishing products by polishing will increase labor costs considerably.
